Casting is the oldest metallurgical technique. The first functional metal components were accidentally refined copper, from chalcopyrite and chalcocite rocks in a fire. The metal could be cast into ingots in the ashes and hammered into a useful shape. Aluminum casting is a critically important group of methods that allow the manufacture of complex parts. The shaping is usually achieved in a single-stage process from liquid metal to finished or near-finished parts. This article will discuss what aluminum casting is, how it works, its importance, types, and applications.
What Is Aluminum Casting?
Aluminum casting is the process of introducing molten aluminum into a cavity to create a part. Aluminum and many of its alloys have relatively low melting points and low viscosity when molten, yet cool to form strong, rigid solids. A variety of casting processes make use of these properties by forming a heat-proof cavity (in one or two parts), into which molten aluminum is poured. The metal then cools and solidifies, taking on the shape of the cavity it has filled. The cavities used for this vary in material and construction, and the processes have various names.
Why Is Aluminum Casting Important?
Aluminum casting is perhaps the most important cluster of technologies and methods in the aluminum product supply chain. Human technology development has gone through seismic shifts over millennia. The bronze age societies were eventually supplanted by those utilizing iron. In turn, iron gave way to steel in the 19th century and steel began to give ground to aluminum in the 1940s. Aluminum is the third most common element in the earth's crust. It’s easy to find its salts in high concentrations—and with energy available, it is straightforward to refine. Aluminum is the key to most areas of technology and aluminum casting is one of the key processes that bring the material into mainstream use and appreciation. The ability to produce net shape-finished parts of high precision, low weight, and moderate strength empowers every manufacturing sector.
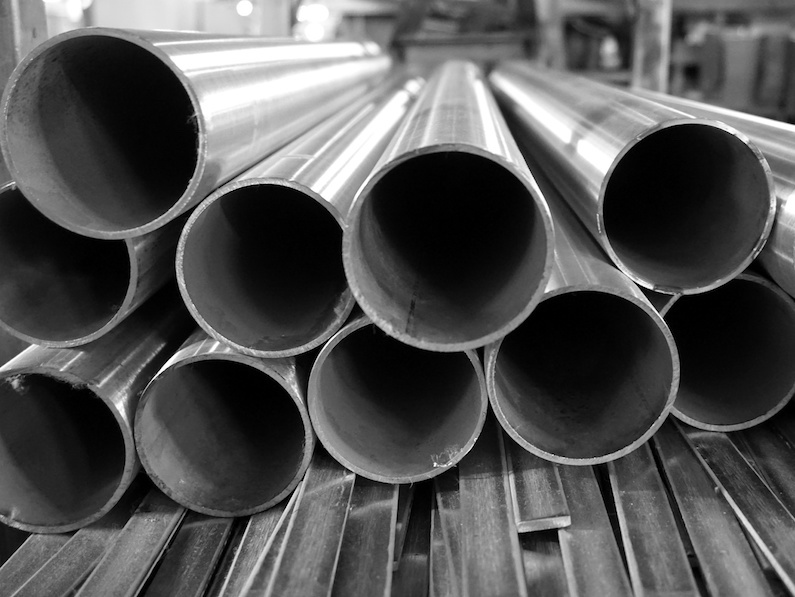
What Are the Properties of Cast Aluminum?
The aluminum used in casting generally refers to its alloys rather than pure aluminum. The properties of which are as follows:
- Aluminum alloys offer a range of ductilities, generally lower than pure aluminum metal which is very soft.
- Ultimate tensile strengths (UTS) vary considerably with the process. Where low porosity is achieved by aggressive degassing of the melt and high-pressure casting, the UTS approaches the optimum for the alloy. Some alloys are developed for greater resilience and others for greater rigidity, implying more tendency to brittleness.
- Higher porosity castings are severely weakened by gas inclusions/cavities that can be common in less controlled approaches. Porosity is a chronic problem for low-pressure aluminum casting.
- Aluminum castings offer an exceptional stiffness-to-weight ratio, only beaten by more costly magnesium or titanium parts.
- Great corrosion resistance is normal in cast aluminum parts.
- Excellent electrical and thermal conductivity.
What Is the Tensile Strength of Cast Aluminum?
Tensile strength is dependent on alloy type, with pure aluminum offering the lowest value. For example, pure aluminum has a tensile strength of 90 MPa while casting alloy A07130 has a value of 221 MPa.